Delta в экструзионном оборудовании с целью повышения качества продукции и сокращения затрат
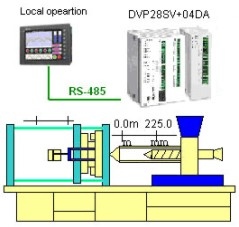
Изготовление изделий из пластика является одной из ключевых задач в легкой промышленности. Производством продукции из пластика занимается огромное число производителей, и их количество постоянно увеличивается. В связи с этим, конкуренция в данной отрасли высока, и производители вынуждены очень строго относится к проблеме максимального сокращения издержек при одновременной необходимости соблюсти качество продукции.
Для выполнения этих двух противоречивых требований экструдер должен быть оснащен хорошей системой управления технологическими этапами производственного процесса, которая бы обеспечила максимально эффективное использование возможностей самой технологической установки, учитывала бы параметры сырья, особенности производимого продукта, смогла бы обеспечить точное соблюдение технических условий изготовления без перерегулирования и недорегулирования.
В общем случае изготовление продукции из пластика подразделяется на следующие фазы: загрузка сырья, механическое перемещение шнеком внутри корпуса экструдера с разогревом, плавлением и перемешиванием сырья до получения рабочей массы, инжекция через фильеру (эксктрузионную головку) с получением изделия нужной формы, охлаждение изделия для получения твердости и выход готового изделия.
Каждый из этапов требует поддержания в соответствующей зоне экструдера определенных давления и температуры, а также максимально эффективной выдержки каждого этапа по времени. Для решения данной задачи компания Delta Electronics предлагает комплектный набор оборудования: программируемый контроллер типа DVP-SA или DVP-SV с модулями аналоговых входов/выходов DVP-AD/DA для общего управления всеми технологическими процессами частотный преобразователь серии VFD-G для регулирования оборотов шнека, а соответственно скорости перемещения материала и рабочего давления в зонах модульный термоконтроллер DTC для получение информации и регулирования температуры в каждой зоне (каждый модуль управляет своим нагревателем) панель оператора для оперативного отображения текущих значений параметров и задания новых
Система управления работает следующим образом:
Программируемый контроллер оперативно получает данные о температуре и давлении в каждой зоне, а также о текущем положении подвижных деталей установки, например при помощи потенциометрических датчиков линейного перемещения. После оперативной обработки данных, контроллер корректирует работу исполнительных устройств: приводного двигателя шнека через частотный преобразователь, нагревательных элементов через модульный термоконтроллер, положение задвижек путем подачи сигналов на электромагниты. Оператор контролирует процесс и вводит параметры посредством человеко-машинного интерфейса (панели). Панель оператора также позволяет загружать готовый набор параметров (рецепты) для контроллера под каждый вид продукции, вести архив данных, выводить предупредительные и аварийные сигналы. Для сокращения количества проводов все устройства связаны последовательным каналом передачи данных по RS485 со скоростью 38400 бит/сек.
Так как изготовление продукции из пластика связано с достаточно сильным нагревом исходного сырья, а затем охлаждением готового изделия, большую долю в производственных издержках составляет расход электроэнергии. Соответственно экономия электроэнергии является одним из основных путей сокращения издержек.
Применение вышеуказанного комплекта оборудования снизит потребление электроэнергии за счет точной дозировки ее подачи в требуемые точки технологической установки. Например, за счет исключения перегревов нагревателей, регулирования скорости вращения шнека путем математической обработки частотным преобразователем VFD-G входных аналоговых сигналов от контроллера и формирования наиболее оптимальной частоты привода, поддержания наиболее оптимальной консистенции рабочей массы, что снижает сопротивление при ее движении внутри корпуса и через фильеру. Отсутствие перегрева сокращает также расход электроэнергии на охлаждение готового изделия.